1. Custom Metal Parts Manufacturing Overview
1. Custom Metal Parts Manufacturing Overview
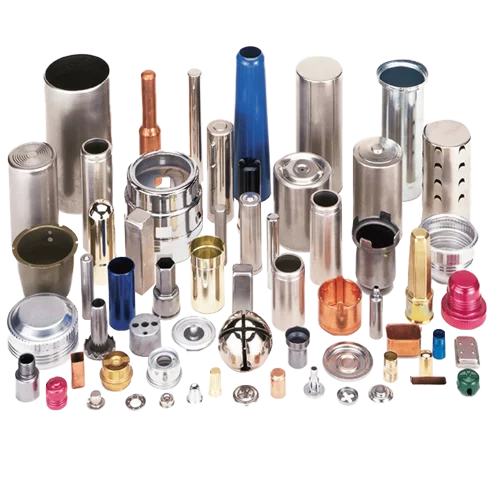
AFI Industrial Co., Ltd is a leading manufacturer of custom metal parts for a variety of industries. Our expertise in precision engineering ensures that we deliver high-quality products tailored to your needs. We have over 12 years of experience in the sheet metal parts industry, and we are experts in a variety of processes including progressive die stamping, transfer die stamping, compound die stamping, and more. Our state-of-the-art facilities are equipped with the latest technology to ensure that your parts are manufactured to the highest standards. Contact us today to learn more about our metal stamping capabilities or to request a quote for your next project.

2. The benefits of using custom metal parts
Section 1:
Customization – One of the primary benefits of working with custom metal parts is that they can produce customized products according to your specifications. This is especially beneficial if you are working on a one-off project or prototype as it allows you to get the exact product that you need without any modifications.
Section 2:
Improved Quality – When you work with metal parts manufacturing, you can also expect to receive products of a higher quality than what you would get from other sources. This is because fabricators have the knowledge and experience needed to produce parts that meet stringent standards.
Section 3:
Reduced Costs – Contrary to what many people believe, working with CNC machining metal parts can actually provide cost-effective solutions and help you save money in the long run. This is because fabricators often offer discounts for large orders, so if you anticipate needing more than one part, it pays to order them all at once.
3. The different types of metal powder parts manufacturers
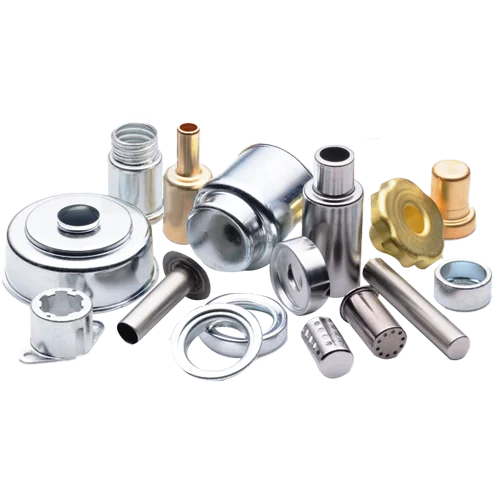
- OEMs – Original Equipment Manufacturers are companies that design and build products or components that are sold to other companies to be used as part of their products. OEMs usually have a large market share in their specific product niche. Examples of OEMs include General Motors, Ford, and Chrysler for automobiles; Boeing, Airbus, and Embraer for commercial aircraft; and Nintendo, Sony, and Microsoft for video game consoles. These metal parts are often used in various industrial applications.
- Job Shop Manufacturers – Job shop manufacturers are small-to-medium-sized businesses that make metal parts to order. They do not have the economies of scale of an OEM, but they are usually more agile and can respond quickly to customer demands. Job shops typically specialize in one or a few manufacturing processes, such as machining, stamping, or fabricating.
- Contract Manufacturers – Contract manufacturers are companies that provide manufacturing services to other companies on a contractual basis. They do not design or sell products under their brand name. Contract manufacturers typically have a significant manufacturing capacity and expertise in a wide range of manufacturing processes. Examples of contract manufacturers include Foxconn and Flextronics.
4. The history of metal parts manufacturing
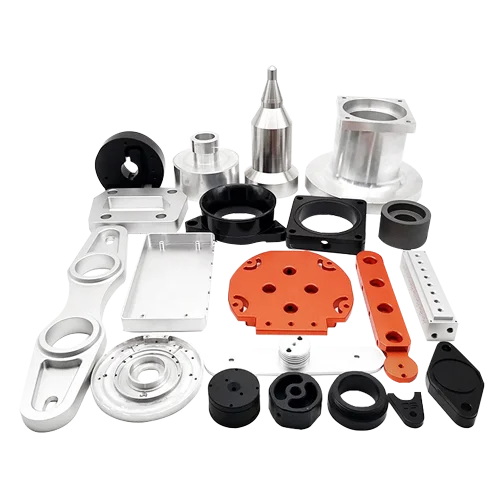
The first-ever recorded metal part was created in ancient Egypt where a gold foil figurine of a cat was found in a tomb. The use of metal parts likely started even before this, however, there are no records to prove it. The first stamped coins were made in China and date back to 640 BC. Around 1200 BC, the Celts were using iron parts for horse bits and stirrups. By 600 BC, blacksmiths around the world were creating tools, horseshoes, and other objects by hand stamping hot metals.
The Industrial Revolution spurred the need for mass-produced items, which resulted in different types of machines being invented for stamping metals. In the 1830s, presses were developed to increase productivity. By 1852, the first steam-powered press was built, which led to an even higher demand for stamped parts. The 20th century brought about new technologies that replaced manual labor with machines. This made it possible to Stamp more intricate designs and create smaller objects. Today, there are many different types of metal stamping machines available that can create objects with extreme precision using advanced manufacturing techniques.
5. Types of metal parts produced
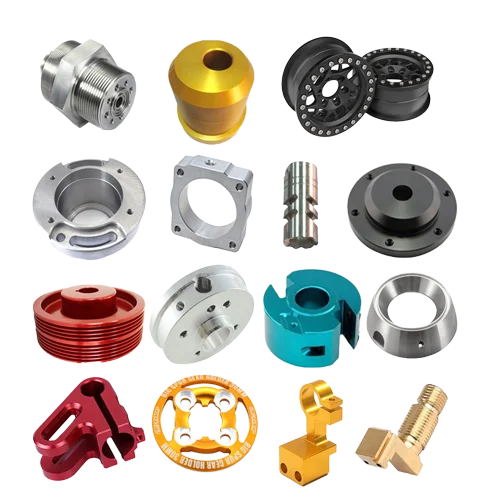
- Aluminum Die Casting
- Magnesium Die Casting
- Zinc Die Casting
Aluminum Die Casting: This type of die casting involves using a non-ferrous metal alloy that has a lower melting point than traditional steel alloys. Due to its lower melting point, it can be cast without the use of a hot chamber machine. Aluminum dies casting
6. How to find the best precision metal fabrication for your needs
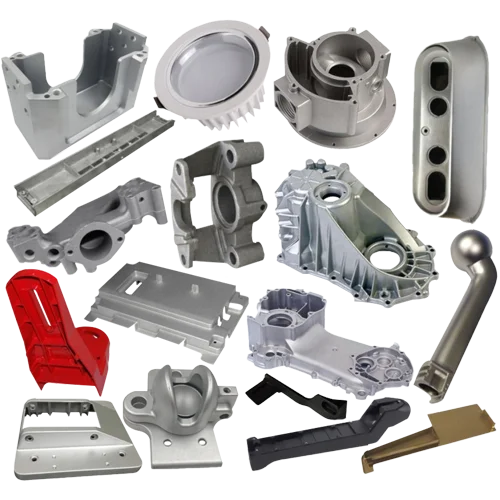
The first thing that you need to do when you are looking for metal injection molding is to figure out what your specific needs are. Do you need a manufacturer that specializes in small parts or large parts? Do you need a manufacturer that can handle high volumes or low volumes? Assessing the production capabilities of potential manufacturers will help you narrow down your search for metal injection molding.
The next thing that you need to do is to look for a metal injection molding that has experience in manufacturing the type of parts that you need. If you need small parts, then you will want to find a manufacturer that has experience in making small parts. If you need large parts, then you will want to find a manufacturer with experience in making large parts. You can usually find this information on the manufacturer’s website.
Another important factor that you need to consider when you are looking for a metal fabrication is their lead time. Lead time is the amount of time it will take for the metal parts manufacturing to make your part and get it shipped out to you. You will want to find a manufacturer with a short lead time so that you can get your parts as soon as possible. Some manufacturers may have longer lead times because they have a backlog of orders, so it is important to ask about the lead time before committing to working with any particular manufacturer.
Finally, you will want to consider the price when you are looking for a metal fabrication. You want to find a manufacturer that can provide you with high-quality parts at a reasonable price. However, it is important to remember that price is not always the most important factor. In some cases, it may be worth paying slightly more for a part from a certain manufacturer if their lead time is shorter or if they have more experience in manufacturing the type of part that you need.
7. Industries Served
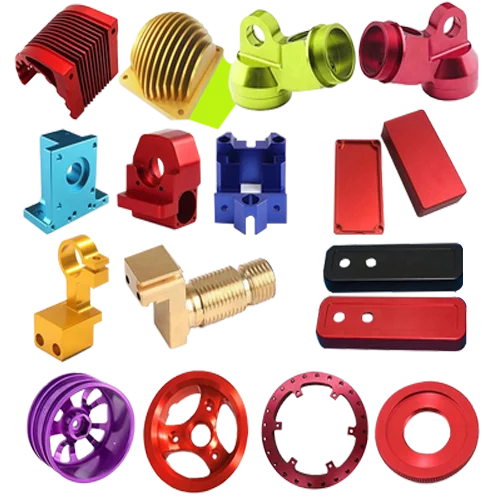
At Company Name, we proudly serve a variety of industries with our metal parts. One of the key sectors we cater to is the aerospace industry. We understand that each industry has its own unique set of challenges and requirements, and we are dedicated to providing the best possible metal fabrication/sheet metal fabrication/CNC machining metal parts/cold rolled steel/hot rolled steel/plastic injection molding to meet those needs.
Below are just some of the industries we serve:
heat treatment
We provide sheet metal/aluminum materials and stainless steel which helps with complex shapes/metal stock/medical equipment
mold cavity
We provide liquid metal/metal sheets that help with other manufacturing processes
cold extrusion
We provide heated metal /liquid material which helps with steel molds/custom parts
custom metal parts
We provide automotive industries /medical equipment which helps with manufacturing services/large-volume production
investment casting
-We provide hot extrusion/cold extrusion/low unit costs which helps with production methods/desired shape/powder coating
desired shape
We provide low-volume casting /surface roughness which helps with steel molds/custom parts
injection molding
We provide heated metal /liquid material which helps with sharp edges/custom parts/rapid prototyping
8. Quality Control
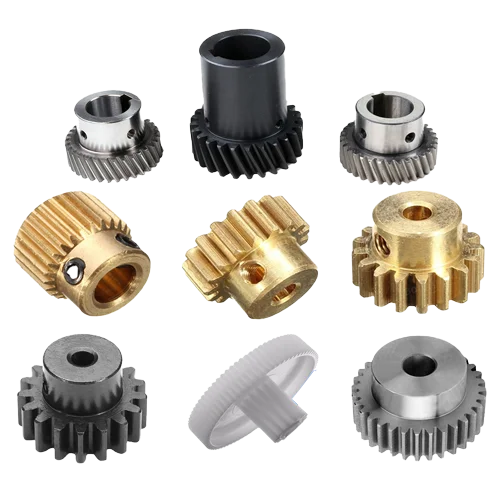
Quality assurance is crucial in maintaining high standards in any industry. Quality control ensures that products meet specific requirements and are free of defects. By implementing rigorous testing and inspection processes, companies can guarantee the reliability and safety of their products.
1. What are the benefits of quality control?
There are many benefits of quality control, but some of the most important ones are listed below:
-It helps to ensure that products and services meet the requirements of the customer or client. For example: CNC machined metal parts and injection molding.
-It helps to prevent defects in products and services. For example: liquid metal and soft metals.
-It helps to ensure that products and services are up to standard. For example: shape metals and chrome plating.
-It can help to increase customer satisfaction. For example: automotive industries and production methods.
-It can help to reduce waste and save money. For example: unwanted materials, non-ferrous materials and hard metals.
2. Why is quality control important?
Quality control is important because it helps businesses to meet the needs of their customers or clients. It also helps businesses to avoid waste, save money, and increase customer satisfaction. If you are thinking about starting a business or if you already have a business, then you should make sure that you have a good quality control system in place.
3. What are some common problems with quality control?
There are many common problems with quality control, but some of the most common ones are listed below:
-Incomplete documentation: This can make it difficult to track progress and identify problems.
-Inefficient processes: This can lead to delays and increased costs.
-Lack of training: This can make it difficult for employees to do their jobs properly.
-Poor communication: This can make it difficult to coordinate efforts and solve problems. How can these problems be avoided?
There are many ways to avoid these problems, but some of the most common ones are listed below: -Make sure that all documentation is complete and up to date.
4. How can companies stay competitive in this industry
1. Stay up to date with the latest technology
2. Offer unique products or services that cannot be easily replicated
3. Automate processes to improve efficiency and reduce costs
4. Foster a culture of innovation within the company
5. Increase marketing efforts to reach new customers
6. Partner with other companies to tap into new markets or share resources
7. Invest in research and development to create new products or services
9. Questions to ask about a potential manufacturing process
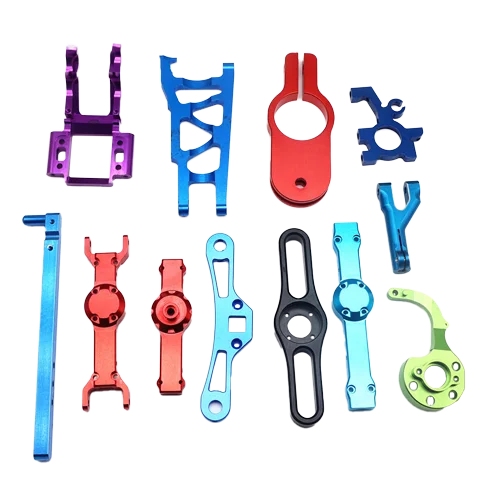
- What is the minimum molten metal order quantity?
- What are the stainless steel metal pipes’ lead times?
What is the price per unit of galvanized steel?
What is stainless steel CNC machining tolerance?
What is the process of metal parts?
Is there a sample available for corrosion resistance?
Can you provide a list of references for polymer-metal mix?
What is your quality control carbon steel process?
Do you have experience with our industry/application/metal particles?
What are your practices for supply chain management?
10. Tips for choosing the right manufacturing process
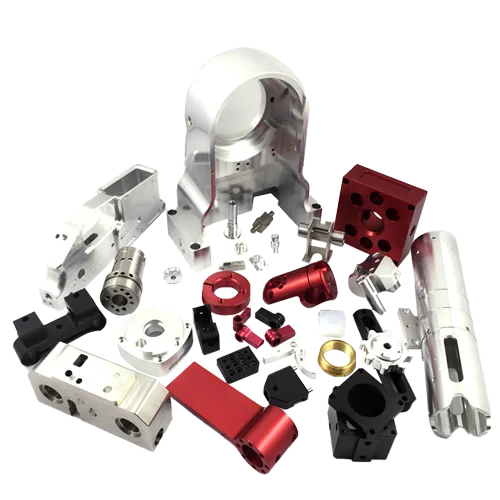
1. Consider their experience.
How long has the company been in business? Have they worked with customers in your industry before? Do they have experience manufacturing the specific type of part you need? The more experience a company has, the more capable it is of handling your project and producing quality machined parts and tooling fabrication.
2. Assess their capabilities.
What kind of machinery and technology do they use? Do they have the ability to produce large quantities of parts quickly, or do they prefer to produce smaller quantities? Make sure their capabilities are in line with your needs. Are they knowledgeable about hard metals and CNC milling
3. Compare price options.
Of course, you’ll want to get quotes from multiple manufacturers before making a final decision. But don’t just blindly compare prices – take the time to understand exactly what is included in each quote and apply a constant cross-section of opinions so you can make a shot peening vs. CNC milling comparison.
4. Ask for references.
Speaking of expectations, be sure to ask the manufacturer you are considering for references so you can get an idea of what kind of results you can expect from their work. A good manufacturing process should have no problem providing references upon request.
11. What are some of the challenges faced by CNC machining metal parts manufacturers?
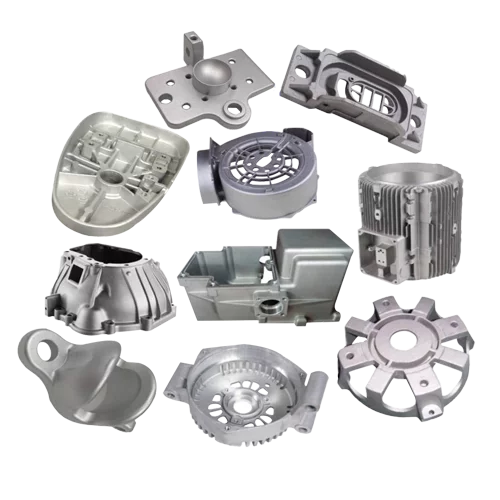
High Cost-effective of Raw Materials
One of the biggest challenges facing metal parts manufacturers is the high cost of raw materials. Steel prices have been on the rise for years, and there’s no end in sight. The tariffs that were imposed on imported steel in 2018 have only made things worse, as domestic producers have been able to raise their prices with impunity. This has put immense pressure on margins, to the point where some manufacturers are struggling to survive.
Skilled Labor Shortages
Another big challenge facing metal parts manufacturers is a skilled labor shortage. There simply aren’t enough people with the training and experience necessary to operate complex wax models or CNC mills metal parts or perform other critical tasks. This shortage is exacerbated by an aging workforce; as baby boomers retire, they take their knowledge and experience with them, leaving a smaller pool of qualified workers behind.
Finally, another big challenge facing metal parts manufacturers is increased competition from abroad. Thanks to globalization, it’s now easier than ever for companies in developing nations to set up shop and start producing products that compete with those from established manufacturers in developed countries like the United States. This increased competition has put immense downward pressure on prices, making it difficult for domestic manufacturers to turn a profit.
To combat this challenge, metal parts manufacturers need to focus on differentiation. They need to find ways to make their products better than those produced by their competitors—whether it’s through higher quality, more innovative design, or better customer service. By differentiating their products in this way, manufacturers can justify charging a premium price that allows them to still turn a profit despite increased competition from abroad.
12. How does a metal parts manufacturer select a supplier?
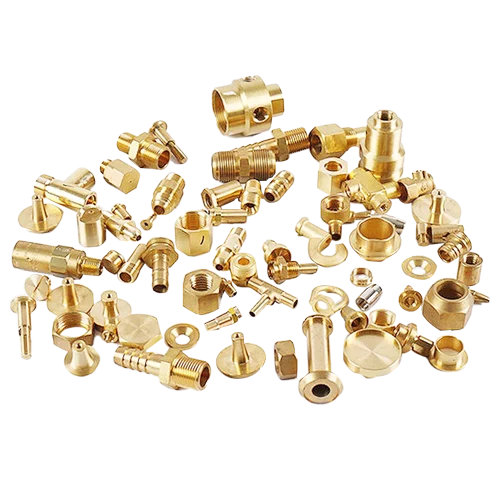
Vendor evaluation is a crucial step for a metal parts manufacturer when selecting a supplier. This process ensures that the chosen supplier meets all the necessary quality and performance standards. By carefully assessing potential vendors, manufacturers can avoid costly mistakes and ensure a smooth production process.
1. certifications & compliance
When it comes to cutting tool manufacturing, compliance is key. You want to make sure that any potential suppliers you consider meet the relevant safety and quality standards for your precision parts, wax patterns, and plastic parts, in addition, you’ll want to make sure they have the necessary certifications needed to operate in your country or region. This will ensure that they can meet your requirements and deliver on their promises.
2. capacity & scalability
Another important factor to consider when selecting a metal parts manufacturer is their capacity and scalability. You’ll want to confirm that they have the necessary resources in place to meet your current and future CNC turning needs. This includes things like staff, equipment, and facilities. It’s also worth inquiring about their process for ramping up production in the event of an increase in demand from your end.
3. cost
Of course, cost-effectiveness is always an important consideration when sourcing suppliers. You’ll want to get quotes from several different manufacturers and compare prices before making a final decision. In addition to the per-unit cost-effective, you should also take into account any other associated costs such as shipping and duties. By taking all of these things into account, you can be confident you’re getting the best possible value for your money and cost-effectiveness.
4. delivery
When it comes to wax patterns and the CNC-turning manufacturing process of precision parts, timing is everything. You need to make sure that the metal parts manufacturer you choose can meet your delivery deadlines. This includes lead time and shipping time and is cost-effective. It’s also worth asking about their process for dealing with delays or other unforeseen circumstances in high-volume production. By having a clear understanding of their delivery process up front, you can avoid any potential disruptions.
13. What Is chemical milling?
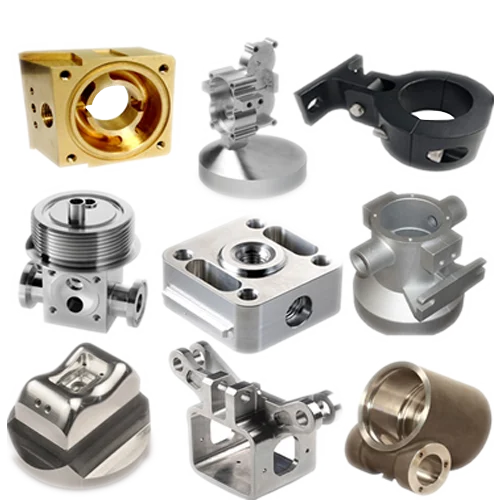
Chemical milling, also known as the etching process, is a thin, flat piece of metal with a thickness that is generally less than 6 mm. It can be made from a variety of metals, including aluminum, steel, titanium, and copper. Sheet metal is used in a wide range of industries and applications, from auto body panels to roofing and siding to HVAC ductwork.
The Properties of Sheet Metal That Make It So Versatile
Sheet metal’s versatility comes from its unique combination of properties. First, sheet metal is strong yet lightweight, making it easy to work with and transport. Second, it can be easily cut, bent, and formed into just about any shape imaginable. Third, sheet metal has excellent weldability and corrosion resistance. Lastly, it’s affordable and can be produced in high volumes without sacrificing quality or precision.
The Different Types of Sheet Metal Processes
Several different types of sheet metal processes can be used to create parts and components from sheet metal. Some of the most common include:
Cutting:
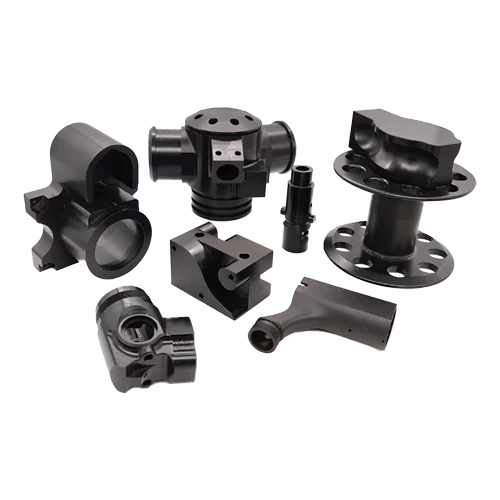
Cutting is the most basic sheet metal process. It involves using a cutting tool (such as a shear or laser cutter) to cut the investment casting out of a larger piece of sheet metal.
Bending:
Bending is a process that involves using heat or mechanical force to deform the metal injection molding into the desired shape. Common bending methods include press brake forming and roll forming.
Drawing:
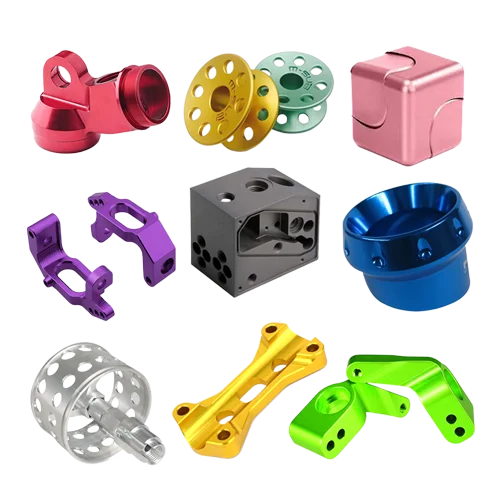
Drawing is a process that uses tension to stretch the metal powder into the desired shape. This process is typically used to create cylindrical shapes like tubes and pipes.
Punching: Punching is a process that uses a die to create holes or other shapes in sheet metal. The die creates works by exerting high amounts of force on the hot extrusion, causing it to deform around the perimeter of the die opening.